KIVO Kosovo,
Kacanik
KIVO Kosovo, established as a joint venture with VM3, is an important link within the KIVO Group. In 2014, we started the construction of a modern plant to optimally add value to products where it was under pressure in Western Europe. Our production site in Kosovo now has more than 100 highly motivated and experienced colleagues and an impressive machine park.
- AddressNational road Ferizaj Kacanik km.14, Pr. Magjistralja, Kaçanik 71000, Kosovo
- Tel. +383 (0)290 170 170
- Mail: info@kivollc.eu
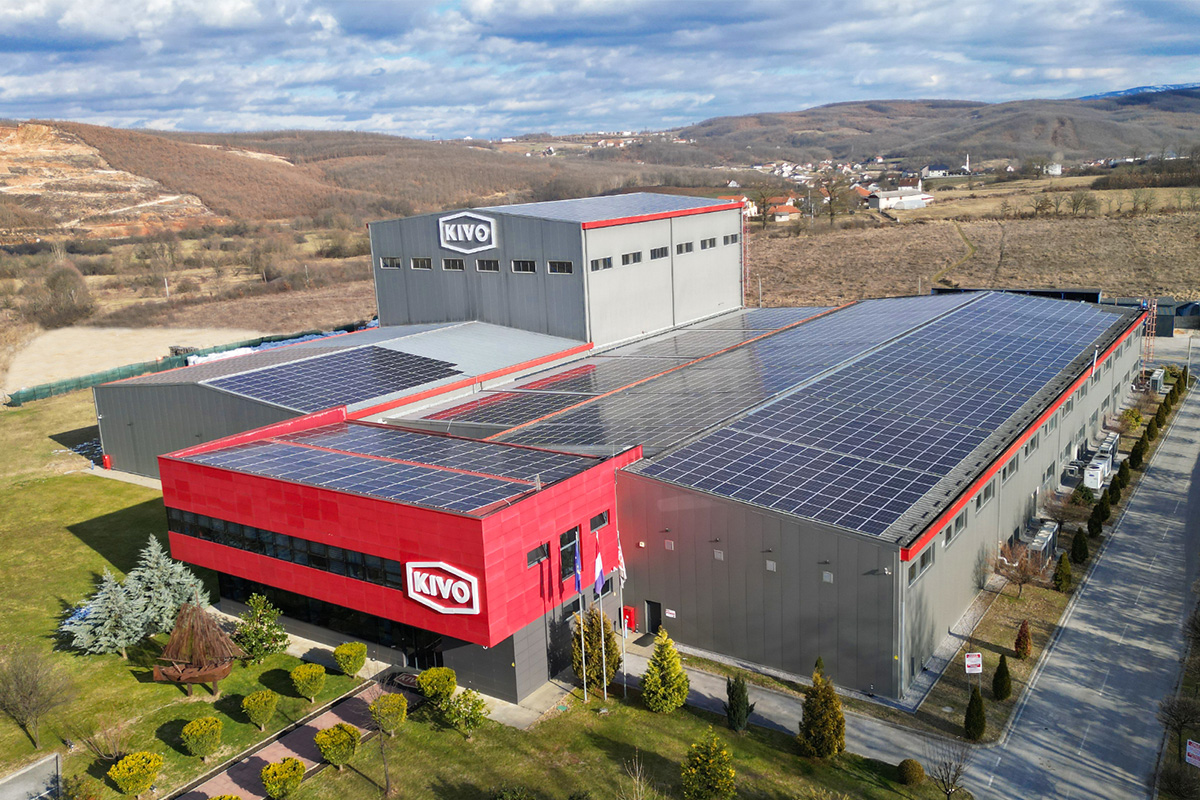
Background KIVO Kacanik
Initial exploratory talks between KIVO and VM3 began in 2013, where a strong click was soon felt. Plans quickly unfolded and a brand new Miraflex Flexo printing machine was ordered in the summer of 2014. Shortly afterwards, construction of a new factory in Kosovo began, with the aim of offering optimal added value for products whose value was under pressure in Western Europe.
After five months of building, moving, installing several production lines and training new employees, the first production could start in early 2015. The factory started with 30 employees and an area of 3,500 m², equipped with four extruders, a flexo printing machine and six sealing machines. In the years that followed, this location continued to expand.
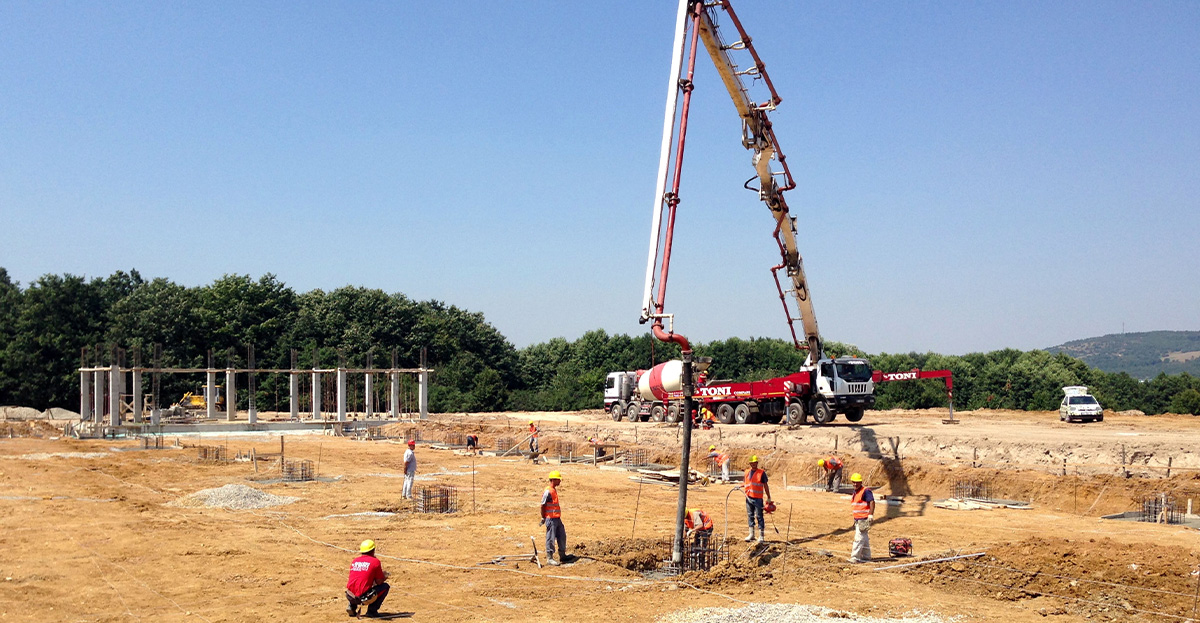
Activities
At KIVO Kosovo, we focus on producing a wide range of high-quality packaging solutions for the European market. Our facilities in Kosovo are equipped with impressive machinery, including 1 Miraflex Flexo printing machine, 1 Coral Flexo printing machine, 8 mono extruders, 1 5-layer coextruder, 4 Hudson Sharp Wicketer bagging machines and 7 sealing machines. This enables us to manufacture various products such as bread bags, waste and collection bags, potting soil film and flower sleeves.
Since its inception in 2014, the factory has expanded significantly, now covering 7,000 m² and employing 115 highly motivated and experienced staff. Our continuous investment in new technologies and the training of local talent ensure that we continue to grow and innovate, always with a focus on quality and sustainability. Thanks to our advanced manufacturing capabilities, we consistently deliver high-quality products that meet the stringent requirements of the European market.
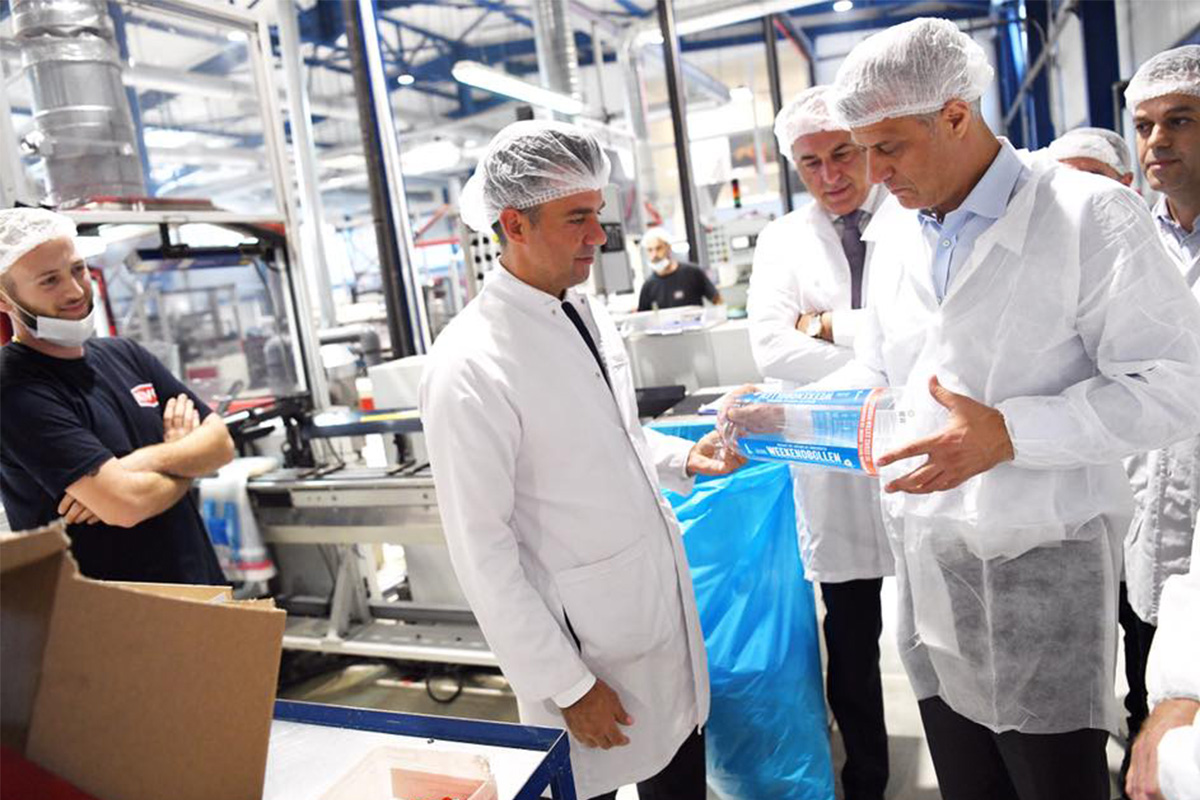
Developments
Since its inception in 2014, the factory has expanded significantly, now covering 7,000 m² and employing 115 highly motivated and experienced staff. Our continuous investment in new technologies and the training of local talent ensure that we continue to grow and innovate, always with a focus on quality and sustainability. Thanks to our advanced manufacturing capabilities, we consistently deliver high-quality products that meet the stringent requirements of the European market.
An important recent development is the installation of hundreds of solar panels on our premises, which now powers our facility with renewable solar energy. This eco-friendly modification demonstrates how sustainability helps us further reduce our carbon footprint. At KIVO Kosovo, we remain committed to a sustainable future while producing high-quality packaging solutions.
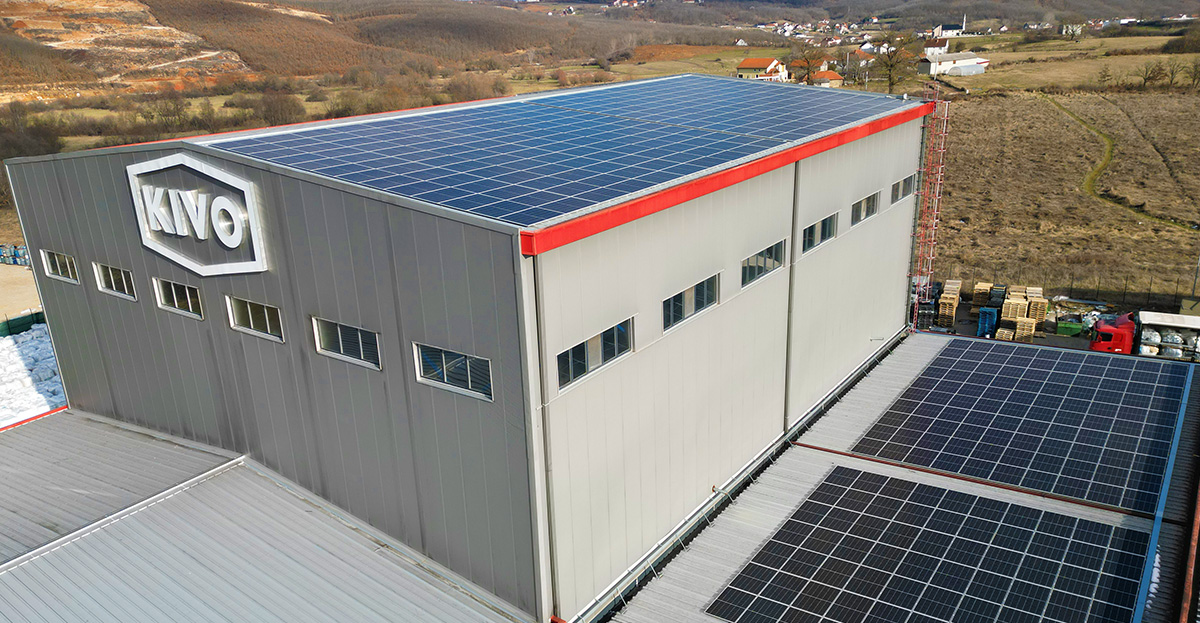
We produce exclusively sustainable packaging solutions
At KIVO Kosovo, we incorporate high percentages of recyclate, sourced from our nearby REKS recycling facility, into our non-food packaging solutions, contributing to a sustainable future.
- 100%
In-house production of PCR
- 100%
Focus on sustainability
Leveraging recyclate and/or making sustainable packaging solutions recyclable.
Widely certified for quality and durability
"*" indicates required fields
We are happy to help
get in touch
We actively contribute to providing high-quality, sustainable plastic packaging and place great value on open communication with our customers, suppliers, and partners. Whether you have questions about our products, want to learn more about our sustainability initiatives, or are interested in a collaboration, we are ready to assist you.
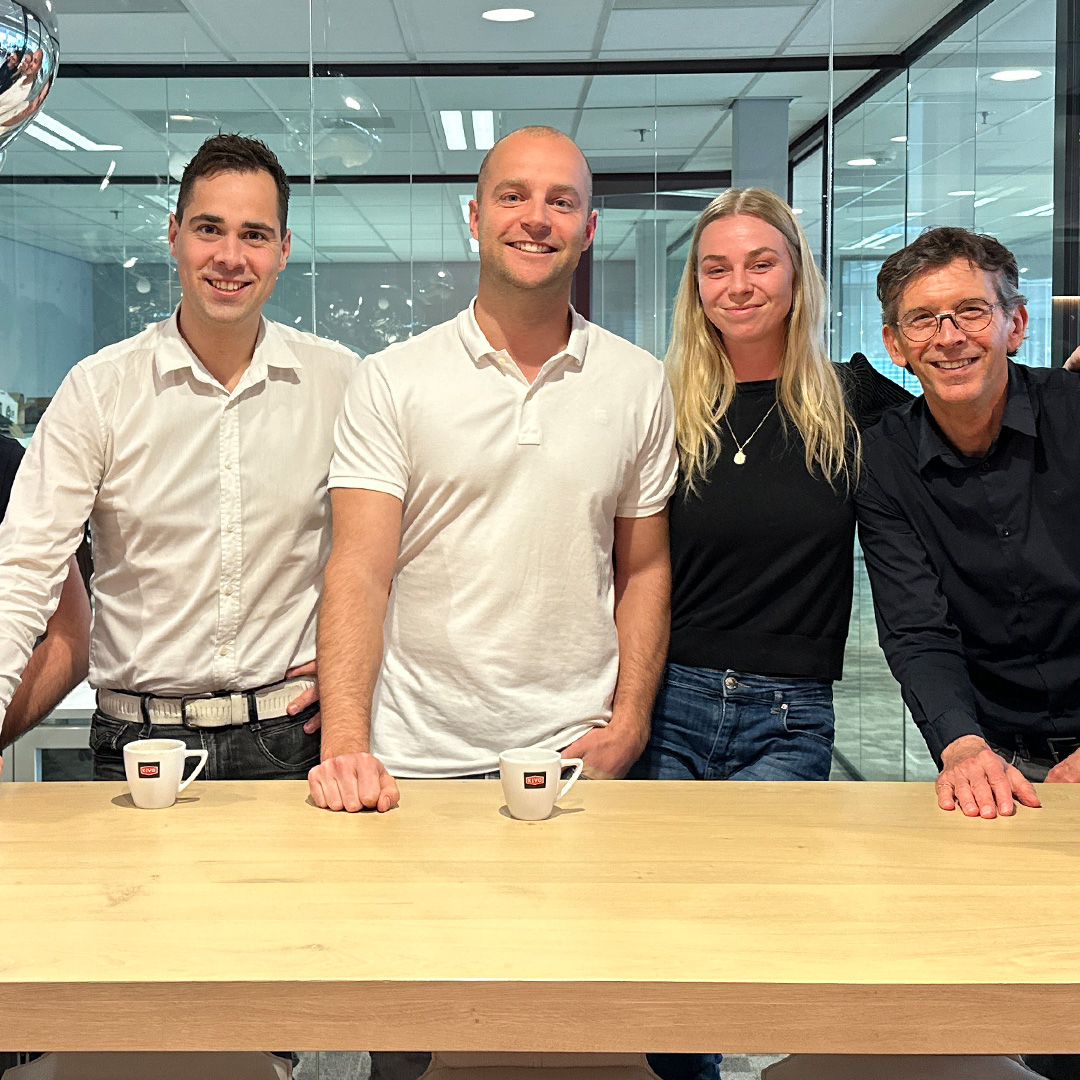
Our colleagues will be happy to assist you!
Our team of experts is ready to answer your questions and help you find the best sustainable packaging solutions.
Get in touch